Posted on Thu, 11/18/2021 - 21:14
By Mark Lowey, CESAR communications advisor
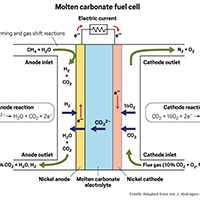
The global cement industry, which emits about 2.3 gigatonnes of carbon dioxide annually (eight per cent of global anthropogenic CO2 emissions), must be decarbonized for the world to achieve net-zero greenhouse gas emissions by 2050.
However, achieving net-zero CO2 emissions in cement production requires major reductions in both process and energy emissions.
A previous CESAR study showed that switching to alternative fuels in a natural gas-fired cement plant doesn’t by itself offer the significant emissions reduction required.
Even switching fuel supply to zero-emission sources would only address 25 to 40 per cent of GHG emissions associated with cement making, since the majority of the CO2 emissions are process-based, resulting from heating the limestone feedstock and releasing embedded carbon.
“We need a technology that can be added to existing cement plants and achieve CO2 reductions of 90 per cent or more,” says Daya Nhuchhen, an energy systems analyst at CESAR.
A new CESAR study, “Towards net-zero emission cement and power production using Molten Carbonate Fuel Cells,” led by Nhuchhen, looked at a possible pathway to cement industry decarbonization using molten carbon fuel cell (MCFC) technology in a natural gas-fired cement plant.
When the cathode of a MCFC is exposed to a flue gas CO2, and the anode is provided with hydrogen, the CO2 moves from the cathode to the anode, creating a concentrated CO2 stream from the anode while generating a substantial electrical current (see illustration below).
Co-authors on the new CESAR study are Song P. Sit, a senior associate at CESAR, and David B. Layzell, CESAR’s director and energy systems architect at The Transition Accelerator, a pan-Canadian non-profit organization focused on developing credible, compelling strategies to accelerate the transition to net-zero energy systems.
Their study examined the impacts of an integrated low-emission cement and power production (LECAPP) system that incorporates external reforming to supply hydrogen at the anode of molten carbonate fuel cell. This enables the MCFC to concentrate the CO2 emissions from a gas-fired cement plant producing 4,200 tonnes per day of clinker. (Clinker, the glassy product of fusing together clay and limestone, is used to make cement).
MCFC technology is commercially available and is already being used by the global power sector.
Figure 1.
The molten carbonate fuel cells made by FuelCell Energy concentrate flue-gas carbon by using CO2 as a working fluid. As described in a recent Chemical & Engineering News article: “At one end, a porous nickel cathode combines CO2, oxygen, and two electrons to make CO32–, the carbonate ion. That CO32– carries the charge through the electrolyte to a nickel anode on the other side, where it reacts with hydrogen to yield water, two electrons, and CO2.”
LECAPP system offers synergistic benefits
The LECAPP system provides synergistic benefits. It not only captures CO2 for geological sequestration, it also produces low-carbon electricity.
The carbon intensity assigned to clinker production – 57 kg of CO2 per tonne of clinker – is a 92-per-cent reduction compared with a clinker plant without carbon management, Nhuchhen notes.
The LECAPP system produced 1,201 kilowatt-hours (kWh) of low-carbon electricity per tonne of clinker produced. This electricity has a carbon intensity of 52 kilograms of CO2 per megawatt-hour (MWh), of which 1,000 kWh per tonne of clinker is available for export to Alberta’s electricity grid.
The exportable electricity has a carbon intensity of only 16 per cent compared with that from a natural gas-fired, combined-cycle power plant.
The LECAPP system’s low-carbon intensity electricity would help decarbonize Alberta’s electricity grid, which currently has a carbon intensity of more than 600 kilograms of CO2 per MWh, Nhuchhen says.
For a cement plant producing 4,200 tonnes per day of clinker, with a LECAPP system producing 174 to 176 MW of grid power, the total CO2 avoided is an estimated 4,030 to 4,048 tonnes per day, according to the CESAR study.
“The large process emissions associated with clinker production means that decarbonization of cement production is particularly challenging. It can’t be solved by simply switching to the use of a zero-emission fuel,” Layzell notes.
“The MCFC technology offers a strategy to capture and concentrate a majority of the emissions while generating low carbon electricity as a second value-added product.”
System provides flexibility, highly efficient CO2 capture
“In terms of energy benefits, the LECAPP system reduced CO2 emissions from both the cement plant and the power sector,” Nhuchhen says.
The LECAPP technology did so without requiring a separate system needing additional energy to capture CO2 associated with its fuel input,” he adds.
Based on a process model of the LECAPP system developed by CESAR researchers, the system requires an energy input of about 1.5 to 5.9 gigajoules per tonne of CO2 avoided, depending on the carbon intensity of electricity that’s displaced. The lowest energy requirement occurs when the electricity from the LECAPP system displaces coal-generated electricity.
This performance is superior to that of other CO2 capture technologies, such as amine-scrubbing which requires thermal energy of about 3.8 to seven gigajoules per tonne of CO2 avoided, Nhuchhen notes.
By using external reformation of gaseous or solid fuels to generate hydrogen-rich synthetic gas for the anode of the fuel cells, the LECAPP system is fuel-flexible. This creates opportunities for using negative-value, waste-derived solid alternative fuels such as plastics.
For example, using plastic waste to generate hydrogen for the molten carbonate fuel cells would divert 144 kilograms of plastics per tonne of clinker produced.
So the LECAPP system would be advantageous for a country such as China, which produces 59 million tonnes-plus of plastic waste per year, Nhuchhen says.
The LECAPP system could be integrated into coal- and petroleum coke-fired cement plants, as well as the power sector or any industrial operation that generates flue gas containing CO2.
When combined with a cement plant producing 4,200 tonnes of clinker per day, the LECAPP system requires a geological storage capacity of 1.9 to 2.2 megatonnes of CO2 per year. Not all nations and regions of the world have potential sequestration sites capable of managing this amount of CO2. But many do, including Western Canada, Indonesia, China, the U.S., Russia and Africa.
“In the global transition to net-zero emissions, it is likely that regions with geological storage capacity will have significant advantage for clinker production,” says the study.
“We need to make sure that we can get the synergistic benefits,” Nhuchhen says. “On the pathway to net-zero, the LECAPP system with MCFC technology gives us a win-win-win solution for the cement industry, the power sector and plastic waste management.”
This CESAR study was supported by LafargeHolcium Inc., Emissions Reduction Alberta, Natural Sciences and Engineering Council of Canada, The Transition Accelerator, and Natural Resources Canada.